Alta Precision ist ein branchenführender Hersteller von Fahrwerken für Verkehrsflugzeuge in Montreal, QC, Kanada. Als sie vor kurzem ihre Produktionsstätte um ein neues Fahrwerksprodukt erweitert haben, war dies eine Gelegenheit, in aktualisierte Funktionen zu investieren.
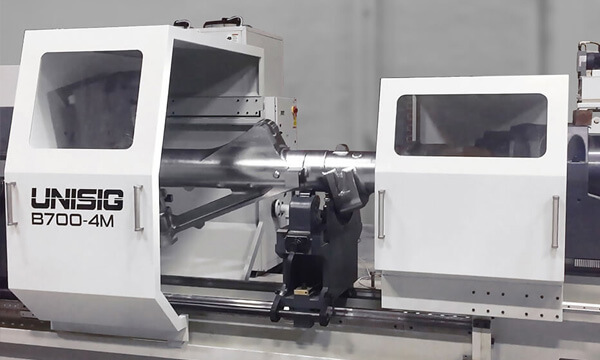
UNISIG meistert die Herausforderungen beim Bohren von Flugzeugfahrwerken
- Posted on
- Anthony Fettig
Branche: Luft- und Raumfahrt
Kundenprodukt: Fahrwerkskomponenten für Verkehrsflugzeuge
UNISIG Lösung: B700 Tiefbett BTA Tiefbohrmaschine
Die Fahrwerksstreben von Alta Precision werden im fertigen Produkt gezeigt.
Alta Precision ist ein branchenführender Hersteller von Fahrwerken für Verkehrsflugzeuge in Montreal, Quebec, Kanada. Als Alta vor kurzem seine Produktionsstätte erweitert hat, um ein neues Fahrwerksprodukt in die Produktion zu integrieren, war dies eine gute Gelegenheit, in erweiterte Fertigungsmöglichkeiten zu investieren.
Alta musste Produktionsausrüstung beschaffen, um die Komplexität der Herstellung von Fahrwerksstreben für die Luftfahrtindustrie zu bewältigen. Von Natur aus sind diese Komponenten hochbelastet, komplex, mit dünnen Wänden in zähen Metallen wie legiertem Stahl 300M. Es wird ein zentrale Tiefbohrung benötigt, die gebohrt und dann innenprofiliert wird.
Bei 230 mm [9 in] im Durchmesser und über 2.100 mm [7 ft] Tiefe, können diese Bohrungen nur auf einer speziellen Tiefbohrmaschine und nicht auf einem konventionellen Bearbeitungszentrum durchgeführt werden. Neben der Hauptaufgabe, diese Bohrungen mit strengen Toleranzen zu bearbeiten, suchte Alta eine Lösung, die ein ergonomisches Setup und einfachen Betrieb ermöglichte, mit der Flexibilität und der Antriebsleistung um eine Vielzahl von komplexen Werkstücken in verschiedenen Längen auf der gleichen Maschine zu handhaben.
Diese Fahrwerksstreben stellen mit asymmetrischen Merkmalen, die einen Schwingkreis von 1.370 mm [54 in] erfordern, und einer exzentrischen Gewichtsverteilung, eine zusätzliche Anforderung dar. Denn zum Erreichen der erforderlichen Geradheit, muss das Werkstück während des Bohrvorgangs gegenläufig zum Bohrwerkzeug gedreht werden. All diese Komplexitäten bestehen in jedem einzelnen Werkstück, die essentiell für das Geschäft von Alta sind.
“In unserer Branche sind wir als Sole Source Lieferant bekannt. Wir sind der einzige Hersteller der diese Werkstücke produziert, also müssen wir liefern”, erklärt Alta-Präsident Guillermo Alonso, “Unser Kunde hat keine Alternative, also können wir uns auch keinen Ausfall leisten. Eine unzuverlässige Maschine zu haben, die nicht liefern kann, wäre für uns keine Option.”
UNISIG entwickelte die ideale Lösung, indem es sein bewährtes B700-Maschinenmodell optimierte, um den spezifischen Anforderungen dieser Anwendung gerecht zu werden und die Anforderungen von Alta an eine leistungsstarke, präzise und effiziente Maschine zu erfüllen.
Die UNISIG BTA-Tiefbohrmaschine B700 setzt auf Gegenlauf von Werkstück und Werkzeug für höchste Genauigkeit und ist für das Vollbohren bis 200 mm [8 in] sowie Aufbohren oder Kernbohren bis 300 mm [12 in] ausgelegt, angetrieben durch automatisches Schaltgetriebe. Die Werkzeugspindel verfügt dabei über einen 94 kW [124 PS] Antrieb, während die Werkstückspindel mit 67 kW [90 PS] angetrieben wird, so dass Alonsos Team jederzeit die nötige Leistung einsetzen kann, um ihre harten Legierungen mit Leichtigkeit und Zuverlässigkeit zu bearbeiten. Hochleistungs-Spindelantriebe liefern diese Leistung bei gleichzeitiger Überwachung der Spindel-Motordrehzahl, um die Drehzahl konstant auf extrem enge Toleranzen zu regeln, unabhängig von der Spindelbelastung.
Das Modell B700 beherrscht wie viele UNISIG Maschinen den BTA Tiefbohrprozess. Daneben aber auch weitere Prozesse wie das Aufbohren und Formbohren, welche bei Alta in der Fertigung der Fahrwerksstreben für die Bohrungsprofilierung eingesetzt werden. Der Maschinenvorschub wird durch 100 mm [4 in] Servo-Kugelgewindetriebe erzeugt, vorgespannt für hohe Steifigkeit und Null-Endspiel, Verbesserung der Standzeit, Tiefenkontrolle und Oberflächenveredelung über mehrere Prozesse, insbesondere Bohrgrundformung. Alle diese Funktionen nutzt Alta in der Fertigung nach höchsten Toleranzstandards und bestätigt so seinen Platz als einer der Branchenführer.
Die Lösung die UNISIG für Alta Precision vorschlug, entwickelte sich aus dieser Maschine, mit Design-Updates, um spezifische Konstruktions- und Leistungsziele zu erreichen, vor allem das Tiefbett-Design, um die extreme Typenvielfalt der unförmigen Fahrwerksstreben aufzunehmen. Das Werkstück-Tiefbett wurde speziell für die von Alta vorgesehene Werkstückpalette entwickelt, ohne jedoch Kompromisse bezüglich Ergonomie der Maschine oder aufwändiger Fundamentierung einzugehen. Werkstückspindel-Orientierung und Verriegelungsfunktion vereinfachen die Werkstückbe- und Entladung durch Starten und Beenden von Zyklen in der praktischsten Orientierung für den Bediener. Die Spindelorientierung ist auch auf der Werkzeugseite verfügbar, so dass das Werkzeug am Zyklusende zurückgezogen werden kann, ohne die perfekte Oberfläche zu beschädigen.
“UNISIG hatte die Flexibilität, auf meine Bedürfnisse zu achten und nahm sich die Zeit mit uns und unseren Konstruktionsanforderungen zu arbeiten”, sagt Alonso. “Sie setzten sich wirklich hin, beteiligten sich aktiv an der Unterhaltung und gaben mir Vertrauen in die Entwürfe auf dem Tisch. Die Maschine arbeitet perfekt.”
Die B700-Tiefbettmaschine erlaubt es dem Bediener, die Werkstücklänge in der CNC-Steuerung zu programmieren, und somit den Werkstückspindelkasten automatisch in die korrekte Position zum BOZA zu verfahren. Der Bediener kann so schnell und einfach Werkstücke einrichten und die Bearbeitung ausführen, gleich welche Varianten gerade bearbeitet werden müssen. Alonso kommentiert auch, dass die Bedienerfreundlichkeit bemerkenswert ist und die gesamte Maschine für Bediener zugänglich ist – Setup, Indikatoren, Bedienelemente, alles was sie brauchen, um höchste Präzision zu fertigen.
Das Team von UNISIG hat das Projekt von Anfang bis Ende begleitet. “Alles kam zusammen und unsere UNISIG Maschine ist nun ein integraler Bestandteil der Fertigungszelle für diese Komponente. Wir haben eine zuverlässige Maschine und einen zuverlässigen Prozess”, bemerkt Alonso. Von der ersten Entwurfsdiskussion über die Konstruktion und Prozessentwicklung bis hin zur Fertigung, Installation und Schulung, “es war alles reibungslos”, sagt er.