Erwähnen Sie Tiefbohrungen, und die meisten Leute denken nur an Bohrmaschinen für die Verarbeitung von Kanonenläufen. Tatsache ist jedoch, dass Tiefbohrungen für eine viel größere Auswahl an Werkstücken gelten
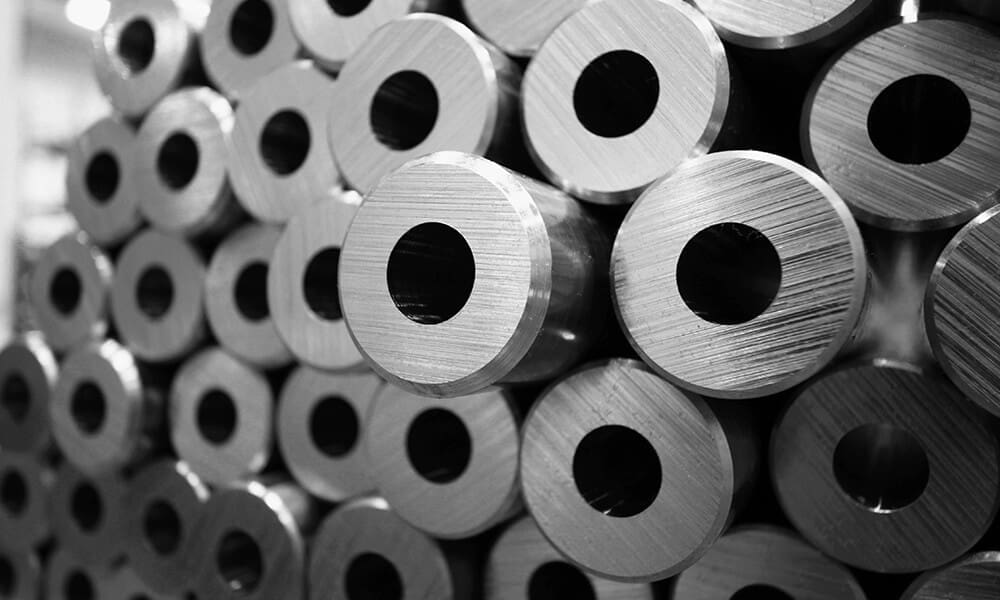
Tiefbohren entwickelt sich weiter
- Posted on
- UNISIG
Von Anthony Fettig, CEO, UNISIG
Zuerst veröffentlicht in Manufacturing Engineering
Erwähnen Sie Tiefbohren, denken die meisten Leute nur an Tiefbohrmaschinen zur Bearbeitung von Gewehrläufen. Tatsache ist jedoch, dass das Tiefbohren für ein viel breiteres Spektrum an Werkstücken eingesetzt wird, die mit herkömmlichen CNC-Bearbeitungszentren normalerweise nicht zu bohren sind.
Wir im Tiefbohrmaschinenbau werden ständig mit neuen und oft einzigartigen Anwendungen konfrontiert, die uns weit über das einfache Tiefbohren hinausführen. So werden beispielsweise in der Medizintechnik Tiefbohrmaschinen zum Bohren von 200 mm tiefen Bohrungen mit 2,5 mm Durchmesser in Titan- und Edelstahlkomponenten eingesetzt. Und obwohl das Tiefenverhältnis von 80:1 bereits ein schwieriger Aspekt der Anwendung ist, machen die erforderlichen engen Toleranzen für Durchmesser und Geradheit den Prozess zu einer echten Herausforderung – und einer, die nur eine Tiefbohrmaschine bewältigen kann.
Eine weitere Anwendung mit kleinen Durchmessern und tiefen Bohrungen ist die Herstellung von Kraftstoffsystemkomponenten. Hersteller von Einspritzdüsenkörpern müssen beispielsweise oft Bohrungen mit einem Durchmesser von nur 1,5 mm und einer Tiefe von 80 mm unter Mehrfachwinkeln bohren, während gleichzeitig eine extrem genaue Position sowie eine spezifizierte Oberflächengüte erreicht werden muss, die entscheidend für einen effektiven Kraftstofffluss ist. Tiefbohrmaschinen bringen zudem Bohrungen mit einem Durchmesser von 9 mm und 250 bis 800 mm Tiefe, in Kraftstoffverteilerrohre ein, wo der Verlauf kritisch ist, um die Kraftstoffdurchgangsbohrungen mit den Hochdruckanschlüssen an jedem Ende auszurichten. Bei Projekten mit Kraftstoffsystemkomponenten werden in der Regel große Teilemengen und Millionen von Bohrungen mit automatisierten Tiefbohrsystemen hergestellt.
Tiefe Bohrungen mit kleinem Durchmesser sind auch in vielen größeren Werkstücken üblich, wie beispielsweise in Kunststoffspritzgusswerkzeugen. Für diese Komponenten erzeugen moderne 5-Achs-Tiefbohr- und Fräszentren heute Dutzende von Kühlkanälen, die in Formwerkzeugkomponenten mit einem Gewicht von 15 Tonnen oder mehr benötigt werden. Die Bohrdurchmesser können von 9 bis 30 mm betragen und bis zu 2.000 mm tief sein. Bei diesen Anwendungen im Formenbau dreht sich alles um Vorschubgeschwindigkeit und Gesamtanlagenproduktivität und die heutigen Tiefbohrsysteme mit dynamischer Fräsleistung reduzieren die Rüstzeiten drastisch und beseitigen Engpässe bei der Bearbeitung in dieser hart umkämpften Branche.
Am anderen Ende des Spektrums verwendet die Luft- und Raumfahrtindustrie Tiefbohrtechnologie, um Bohrungen mit großen Durchmessern in Werkstücken zu erzeugen, darunter Präzisionsaktuatoren, Turbinenwellen und Fahrwerkskomponenten wie Fahrwerksgabeln, Achsen und Träger aus speziellen legierten Stählen und Titan.
Für die Anwendung in der Produktion einer Fahrwerksgabel hat Unisig jüngst eine Tiefbohrmaschine mit 1.600 mm Umlauf über dem Bett entwickelt. Die Maschine erzeugt Bohrungen bis zu einem Durchmesser von 220 mm und einer Tiefe von bis zu 4 m. Zusätzliche Aufbohrschritte und Formbearbeitung des Bohrgrunds vergrößern den Innendurchmesser auf 240 mm, mit engen Durchmessertoleranzen und kritischer Übergangsgeometrie zwischen den Bohrungen.
Eine weitere Anwendung bei extremen Tiefbohrungen sind Schwerstangen, die in der Öl- und Gasexploration eingesetzt werden. Diese Werkstücke haben typischerweise eine Länge von etwa 10 m und erfordern äußerst genaue Bohrungen mit einem Durchmesser von 30 bis 80 mm. Die Werkstoffe sind legierter Stahl oder Inconel und erfordern spezielle Werkzeuge und Maschinen, um sehr gerade Bohrungen durch die Länge der Schwerstangen einzubringen.
Fortschritte im der Werkzeugtechnologie haben zu Tiefbohrmaschinen geführt, die mit mehr High-End-Funktionen ausgestattet sind als je zuvor.
Komponenten für Instrumentierung, die bei der Ölexploration eingesetzt werden, dehnen die Grenzen der heutigen Möglichkeiten von Tiefbohrmaschinen. Anfragen nach 4 m tiefen Bohrungen mit 8 mm Durchmesser sind keine Seltenheit, und Unisig hat hochspezialisierte Maschinen mit fortschrittlicher Bewegungssteuerung und Prozessüberwachung entwickelt, um diese speziellen Anforderungen zu erfüllen.
Die gestiegene Kundennachfrage nach branchenspezifischen Bearbeitungsmöglichkeiten sowie die Weiterentwicklung der Werkzeuge haben zu Tiefbohrmaschinen geführt, die mit mehr High-End-Funktionen als je zuvor ausgestattet sind, und dies umfasst bereits Maschinen der Einstiegsklasse. Die kostengünstigen UNE-Maschinen von Unisig verfügen beispielsweise über die gleiche Prozesssteuerung, Echtzeit-Rückmeldung der Schnittparameter, grafische Datenprotokollierung und andere Weiterentwicklungen, die ursprünglich für extreme High-End-Systeme von Großprojekten entwickelt wurden.
Tiefbohrmaschinenhersteller wie Unisig heben ihr Technologieniveau weiter an und erweitern damit das Anwendungspotenzial des Tiefbohrverfahrens. Die heutigen Tiefbohrmaschinen sind hochentwickelte schlüsselfertige Systeme, die Leistung und Prozessstabilität weit über die Möglichkeiten der einfachen Tiefmaschinen der Vergangenheit hinaus gewährleisten.