Mai
USC-M38 zeigt Wirkung im Formenbau
- 2015
- UNISIG
Branche: Formenbau, Automobilindustrie
Kundenprodukt: Kunststoff-Spritzgußwerkzeuge
UNISIG Lösung: USC-M38 Tiefbohr- und Bearbeitungszentrum für den Formenbau
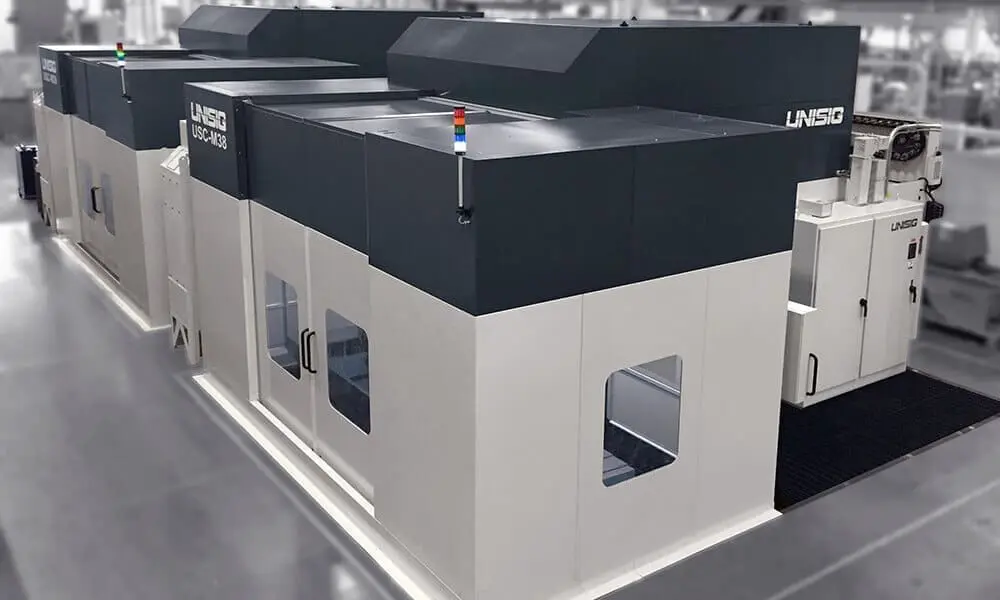
Mai
Branche: Formenbau, Automobilindustrie
Kundenprodukt: Kunststoff-Spritzgußwerkzeuge
UNISIG Lösung: USC-M38 Tiefbohr- und Bearbeitungszentrum für den Formenbau
Mrz
Branche: Offroad und Landwirtschaft
Kundenprodukt: Hydraulikzylinder
UNISIG Lösung: S600 Schäl- und Glattwalzmaschine
John Deere, ein weltweit führendes US-Unternehmen, das Hochleistungshydraulikzylinder herstellt, modernisierte seine Zylinderproduktion, die zur Herstellung von über 700 einzigartigen Zylindermodellen benötigt wird. Die Anforderungen an die Oberflächengüte und die Produktionsmenge waren Schlüsselfaktoren, die für alle Zylinderdurchmesser und -größen von entscheidender Bedeutung waren.
Die Lösung von UNISIG umfasste anwendungsspezifische Dienstleistungen sowie Maschinen, Werkzeuge und Zubehör, um die Ziele des Kunden zu erreichen und gleichzeitig eine beispiellose Oberflächengüte zu erreichen. Daneben umfangreiche Schulungen für Ingenieure und Bediener, damit der Kunde seine Anforderungen an die Zylinderfertigung in dieser herausfordernden Produktionsumgebung erfüllen kann.
Der Projektumfang besteht in einem ersten Schritt aus sieben UNISIG S600-Maschinen für die Bearbeitung von Innendurchmessern bis 200 mm Durchmesser und einer Länge bis 3.000 mm, die sowohl in den USA als auch in Mexiko installiert sind, wo sie derzeit in Betrieb sind und die Anforderungen der Hydraulikzylinderfertigung erfüllen.
Aug
Von Derek Korn, Senior Editor
Ursprünglich veröffentlicht in Modern Machine Shop, August 2012
Damit ein Hydraulikzylinder effektiv arbeiten kann, muss der Innendurchmesser des Zylinders präzise rund und spiegelglatt sein, um eine gute Abdichtung zwischen ihm und dem passenden Innenkolben zu gewährleisten. Dies wird üblicherweise durch Schälen und anschließendes Glattwalzen in einem rohrförmigen Werkstück erreicht. Beim Schälen werden Hartmetallklingen verwendet, die um den Durchmesser eines Werkzeugs positioniert sind, um Späne abzutragen und eine geometrisch runde Bohrung zu erzeugen. Beim Glattwalzen, einem Kaltumformprozess, werden mehrere Walzen eingesetzt, um die nach dem Schälen zurückgebliebenen Materialspitzen zu komprimieren und eine extrem glatte Oberfläche zu erzielen. Durch das Glattwalzen wird auch eine Verdichtungsschicht in die Zylinderwand eingebracht, wodurch die Lebensdauer des Zylinders verbessert wird.
Diese Vorgänge werden manchmal in einem Durchgang mit einem kombinierten Schäl- / Glattwalzwerkzeug auf einer BTA-Tiefbohrmaschine ausgeführt. UNISIG, ein Anbieter von Maschinen, Werkzeugen und Automatisierung für Tiefbohranwendungen, hat unlängst Maschinen entwickelt, speziell für das Schälen und Glattwalzen und dabei die steigende Nachfrage für diese Maschinen bei Herstellern von Hydraulikzylinden festgestellt. Die Maschinen der S-Serie verwenden für beide Arbeitsvorgänge ein einziges Werkzeug und erreichen Rundheitstoleranzen von IT-8 oder IT-9 sowie Bohrungsoberflächen von bis zu Ra 0,05 bis 0,2 Mikron in einer Aufspannung und einem Werkzeugdurchgang.
Laut Sarang Garud, Anwendungstechniker bei UNISIG, basieren 80 Prozent des Maschinendesigns der S-Serie auf den vorhandenen BTA-Tiefbohrmaschinen der B-Serie des Unternehmens. Trotzdem stellt er drei unterschiedliche Merkmale fest, die es der S-Serie ermöglichen, beim Schälen und Glattwalzen hocheffektiv zu sein:
Die für Hydraulikzylinder verwendeten Rohre sind relativ dünnwandig. Es muss darauf geachtet werden, dass das Rohr fest genug für das Schälen und Glattwalzen gespannt ist, jedoch nicht so fest, dass es sich verformt. Daher werden normalerweise Spannkonen eingesetzt, um die Rohre an beiden Enden anstelle von Dreibackenfuttern zu halten. Diese Spannmethode ermöglicht auch einen schnellen Werkstückwechsel in automatisierten Umgebungen. Darüber hinaus muss aufgrund des inhärent hohen Länge zu Durchmesser Verhältnisses dieser Werkstücke eine zusätzliche Unterstützung entlang der Länge des Rohrs bereitgestellt werden. Die S-Serie verwendet eine V-förmige hydraulische Zentrierspanner, um diese Werkstückunterstützung bereitszustellen.
Beim Schälen werden dünne Schnitte gemacht. Der radiale Eingriff eines Schälmessers in das Werkstück kann nur 2 mm betragen, und die Vorschübe können 1 mm pro Umdrehung und Schneide betragen. Jedes Werkzeug verfügt jedoch über zwei oder drei Schälmesserklingen, wodurch sich die effektive Vorschubgeschwindigkeit vervielfacht. In ähnlicher Weise erfordert der Kaltumformprozess Glattwalzen ein hohes Drehmoment und hohe Spindeldrehzahlen, da er die Spitzen, die das Schälen hinterlässt, plastifiziert und verichtet. Infolgedessen verfügt die S-Serie über einen robusteren Antriebsstrang mit Motoren mit höherer Leistung und schnelleren Spindeldrehzahlen als herkömmliche BTA-Tiefbohrmaschinen.
Ein Hydraulikkreis im Inneren des Schäl- und Glattwalzwerkzeugs steuert die Schälmesser und Walzen während des Bearbeitungsvorgangs aus. Daher hat die S-Serie am hinteren Ende des Werkzeugspindelkastens eine Drehdurchführung, um eine hydraulische Verbindung über die gesamte Länge des rotierenden Werkzeugs herzustellen. Sobald der Bearbeitungsdurchgang abgeschlossen ist, werden die Klingen und Walzen in das Werkzeug zurückgezogen, damit es durch das neu gefertigte Hydraulikrohr zurückgezogen werden kann. Das Werkzeug dreht sich beim Rückzug weiter, aber Nylonführungen am Werkzeug und die kontinuierliche Kühlmittelzufuhr verhindern eine Beschädigung der Zylinderoberfläche.
Die Maschinen der S-Serie sind für Schäl- und Glattwalzdurchmesser von 40 – 300 mm (1.5 bis 12 “) und für Längen bis 13 m (20 ‘) erhältlich (weitere Maschinen auf Anfrage). Die Maschinen können auch modifiziert werden, um BTA-Bohren-, Aufbohren, sowie andere Bohr- und Rohrbearbeitungsvorgänge durchzuführen. Darüber hinaus können Werkzeuge so konfiguriert werden, dass sie Rohrbearbeitung in einer Vielzahl von Werkstoffen durchführen können.
Die Maschinen der S-Serie sind für den Einsatz von kombinierten Schäl- und Glattwalzwerkzeugen ausgelegt um geometrisch runde Bohrungen mit hochwertiger Oberfläche in Werkstücken wir Hydraulikzylindern herzustellen.
Rollieren erzeugt eine hochglanzpolierte Oberfläche mit Glätte bis Ra 0,05 Mikron.
Jun
Von Mark Albert, Editor-In-Chief
Zuerst veröffentlicht in Modern Machine Shop Online
Das Zieh-Aufbohren ermöglicht eine bemerkenswerte Geradheit beim Tiefbohren. Eine Variante dieser Technik ist auch dann sinnvoll, wenn die Einhaltung einer konstanten Wandstärke (z. B. bei langen (Schleider-) Gussrohren) oberste Priorität hat.
Da in vielen Anwendungen das effektive und effiziente Tiefbohren entscheidend ist, gehört die Tiefbohrtechnologie zu den am weitesten entwickelten Bereichen der Metallbearbeitung. Es umfasst eine Vielzahl von Prozessen und Methoden. UNISIG (Menomonee Falls, Wisconsin), ein Anbieter von Maschinen, Werkzeugen und Automatisierung für die Tiefbohrbearbeitung berichtet, dass die Liste der von ihm bedienten Industrien die Luft- und Raumfahrt, Automobilindustrie, Verteidigung, Hydraulik, Formenbau, Öl- und Gaseploration sowie Energie umfasst. Die Tiefbohrfertigung ist jedoch weitgehend die Domäne von Betrieben, die sich auf diese Bearbeitung spezialisiert haben, während Technologieanbieter wie UNISIG glauben, dass ein breiteres Bewusstsein für Tiefbohrherstellungsverfahren neue Benutzerkreise auf wertvolle Fertigungsmöglichkeiten aufmerksam machen würde.
Als Beispiel dafür, wie die Tiefbohrtechnologie einige ihrer extremsten Herausforderungen gemeistert hat, weist UNISIG auf eine besonders interessante Technik hin: das Zieh-Aufbohren, mit dem Anwender bemerkenswerte Geradheiten in tiefen Bohrungen erzielen können. Eine Variante dieser Technik ist auch dann sinnvoll, wenn die Einhaltung einer konstanten Wandstärke (z. B. bei langen (Schleuder-) Gussrohren) oberste Priorität hat.
Wie der Name schon sagt, wird beim Zieh-Aufbohren ein Schneidwerkzeug durch eine vorhandene Bohrung gezogen. Das Zieh-Aufbohren wird normalerweise auf derselben Maschine durchgeführt, mit der die ursprüngliche Bohrung eingebracht erstellt wurde. In diesem Fall wird ein Bohrrohr ganz durch die vorhandene Bohrung gesteckt. Nach dem Austritt am gegenüberliegenden Ende wird das Rohr mit einem einschneidigen Zieh-Aufbohrkopf ausgestattet. Anschließend wird das Bohrrohr mit der Werkzeugspindel verbunden und durch das Werkstück zurückgezogen. Das Bohrrohr dreht sich dabei in eine Richtung, während das Werkstück von der Werkstücksspindel in die entgegengesetzte Richtung gedreht wird. Der Werkzeugkopf hält eine Hartmetallschneidplatte der entsprechenden Sorte und Ausführung für das Werkstückmaterial. Diese Wendeschneidplatte funktioniert ähnlich wie ein Innendrehmeißel, indem sie die ursprüngliche Bohrung beim Einziehen in das Werkstück leicht vergrößert. Kühlmittel, das um das Bohrrohr gepumpt wird, fließt durch das innere des Rohrs nach außen, um die Späneabfuhr zu unterstützen und die Oberfläche zu schützen.
Laut Sarang Garud, einem Anwendungstechniker bei UNISIG, kann der beim Ziehaufbohren erzielte Mittenverlauf weniger als 0,08 mm/Meter (0,001 Zoll pro Fuß) Werkstücklänge betragen, wenn Material, Werkzeug und Prozessbedingungen günstig sind. Um diesen Grad an Geradheit zu erreichen, können jedoch mehrere Durchgänge erforderlich sein.
Für die Rundlaufgenauigkeit wird anstelle eines einschneidigen Werkzeugs ein mehrschneidiger Ziehaufbohrkopf verwendet. Ein Mehrschneidwerkzeug hat normalerweise zwischen zwei und sechs Wendeschneidplatten, sagt Herr Garud. Vor den Wendeschneidplatten befinden sich Führungsleisten, damit der vorhandene Innendurchmesser der Bohrung beim Schneiden Halt bietet. Im Gegensatz dazu wird ein einschneidiger Werkzeugkopf in der fertigen Bohrung abgestützt und geführt, sodass sich hinter der Wendeschneidplatte Führungsleisten befinden.
Herr Garud merkt an, dass das das ziehende Bohren mehrere Varianten umfasst. Zum Beispiel ist es üblich, die Pilotbohrung einzubringen, indem man bis zur Mitte des Teils bohrt, es dann dreht und die zweite Hälfte der Bohrung erzeugt. Diese Vorgehensweise verringert den Gesamtmittenverlauf der resultierenden Bohrung, da jede Hälfte der Bohrung im Vergleich zu einer Bohrung die in einem einzigen Durchgang vollständig gebohrt wurde, weniger Verlauf zeigt. Somit hat das Zieh-Aufbohren bereits einen „Vorsprung“ beim Richten.
Das Ziehbohren kann auf jedes Werkstück angewendet werden, das eine Tiefbohrmaschine aufnehmen kann. Die einzige Begrenzung der Teilelänge ist die mögliche Länge auf der Tiefbohrmaschine. Ebenso profitiert das Zieh-Aufbohren von den gleichen Qualitäten wie der Genauigkeit und Steifigkeit in der Tiefbohrmaschine, die sich auf den ursprünglichen Bohrvorgang auswirken. Darüber hinaus ermöglicht die automatische Erfassung der Geschwindigkeit und des Drucks des Kühlmittelflusses den Bedienern, Werkstücke und Schneidwerkzeuge zu schützen, indem die Schneidbedingungen während des Zieh-Aufbohrens genau überwacht werden.
Ein besonderes Zubehör, das das Zieh-Aufbohren effizienter macht, ist die Laterne. Eine trommelförmige Vorrichtung mit Öffnungen auf gegenüberliegenden Seiten, die Laternene wird am Werkstückspindelende der Maschine montiert. Die seitlichen Öffnungen erleichtern die Montage und Ausrichtung einer Führungsbuchse für das Zieh-Aufbohrwerkzeug. Durch die Laternene entfällt auch die sonst erforderliche spezielle Vorbohrung, damit das Zieh-Aufbohrwerkzeug mittig in das Werkstück eindringt.
Fortschritte in der Tiefbohrtechnologie werden die Leistungsfähigkeit von Fachbetrieben stärken und gleichzeitig ihren Einsatz in der allgemeinen Metallbearbeitung erweitern. Durch die Bereitstellung kompletter Bearbeitungssysteme, Werkzeuge, Kühlmittel, Zubehör und Prozess-Know-how ist UNISIG bereit, Kunden bei beiden Trends zu unterstützen.
Obwohl Tiefbohrmaschinen wie diese B630 von UNISIG für die besonderen Anforderungen beim Bohren von langen Werkstücke entwickelt wurden, verfügen sie dennoch über die Flexibilität, eine Vielzahl von Operationen wie Bohren, Aufbohren, Kernbohren, Glattwalzen und Zieh-Aufbohren durchzuführen.
Zieh-Aufbohren ist eine Präzisionsbearbeitung, bei der ein Schneidwerkzeug durch eine vorhandene Bohrung gezogen wird, um die Geradheit zu verbessern.
Mai
Ursprünglich veröffentlicht in Moldmaking Technology, March 2014
Formenbauer, die das Potenzial von Technologie und Ausrüstung erkennen und sowohl auf Genauigkeit als auch auf Produktivität abzielen, erhöhen ihre Wettbewerbsfähigkeit auf dem Markt. Der Schlüssel liegt im Einsatz von Maschinen, die so konstruiert sind, dass sie die zeitaufwändigen Elemente des Formenbaus reduzieren, gleichzeitig die Qualität und die Genauigkeit verbessern und die Möglichkeit menschlicher Fehler ausschließen.
Der Formenbauprozess befasst sich mit einer herausfordernden Kombination von Bearbeitungstoleranzen, die durch langwierige Werkstückeinrichtungsschritte noch komplizierter wird, die es der Maschine ermöglichen, über Bearbeitungs- und Bohrschritte hinweg präziser mit dem Werkstück zu interagieren.
Maschinen, die für bestimmte Herausforderungen im Formenbau entwickelt wurden – beispielsweise der Steigerung des Durchsatzes durch Eliminierung vieler wichtiger zeitintensiver Elemente bei der Herstellung einer Form – sind eine optimale Lösung für Formenbauer, die sich einen Wettbewerbsvorteil verschaffen möchten. Diese Maschinen verfügen über Funktionen, die den Bedarf an kostspieligen Vorrichtungen und erweiterten Umrüstungen verringern und eine einzige Werkstückeinrichtung für mehrere Bearbeitungsprozesse ermöglichen, während Operationen auf allen vier Seiten eines Werkstücks ausgeführt werden können.
Eine Form auf einer solchen Maschine kann unter Verwendung eines geschruppten Werkstücks hergestellt werden, das mit modularen Nullpunkt-Spannkomponenten auf dem Tisch aufgenommen wird. Das Werkstück wird vierseitig gefräst und mit Hochleistungseinlippenbohrern und BTA-Werkzeugen mit sehr hohen Vorschüben gebohrt. Mit dem gleichen Setup und in der gleichen Aufspannung können Bearbeitungen unter Mehrfachwinkeln, sich überschneidende Bohrungen, Taschen und komplexe Oberflächenbearbeitung präzise und effizient durchgeführt werden. Anschließend können kritischen Merkmale automatisch vermessen werden. Das spart dem Formenhersteller Tage an Produktionszeit.
Eine leistungsfähige Maschine erfüllt auch die hohen Toleranzanforderungen komplexer Formprofile. Zu den Merkmalen, die dazu beitragen, gehört ein steifer B-Achsen-Tisch, der schwere Werkstücke aufnehmen kann, sowie eine hohe Momentenbelastung. Ein weiteres wesentliches Merkmal ist ein Spindelkasten, der Fräs- und Bohrspindeln trägt, die ohne Minimierung der Steifigkeit auf einer A-Achse kippen können und eine Drehung der B-Achse in extremen Winkeln und deutlich größere als die üblichen Verfahrwege ermöglichen. All dies führt dazu, dass mühsame Umrüstarbeiten entfallen, was wertvolle Zeit und Aufwände ersparen kann, die dann für den Einsatz fortschrittlicher Technologie und die Produktion besserer Formen aufgewendet werden können.
Maschinen, die eine Reihe von Bearbeitungs- und Bohrvorgängen kombinieren, einschließlich Hochleistungsfräsen und Tiefbohren, können die Effizienz weiter steigern. Sie verfügen über mehrachsige Positionierung und sind mit leistungsfähigen Spindelkästen mit Getriebe und Cat50-Spindeln ausgestattet. Eine Spindel für konventionelles Einlippen-Tiefbohren als auch für BTA-Hochleistungstiefbohren, mit fünf- bis siebenmal höheren Vorschüben als beim Einlippen-Tiefbohren, ermöglicht die Produktivität weiter zu steigern bei gleichbleibender Genauigkeit.
Zudem nutzen die hochproduktive Maschinen alle Möglichkeiten zur Automatisierung des Bearbeitungsprozesses und sind in dynamischen Situationen unabhängig von der Achsenausrichtung äußerst genau. Diese Maschinen sind in der Regel mit verschiedenen nützlichen Optionen ausgestattet, wie z. B. Glasmaßstäbe und Drehgebern mit direkter Rückkopplung. Sie können auch die Vorteile von Volumenkompensation mit einer Standard-Kontursteuerung nutzen. So ermöglichen Werkstückabtastung, Werkzeug-Laservoreinstellung und automatische Werkzeugwechsler mit einer großen Anzahl von Platzen einen unbeaufsichtigten Betrieb mit größerer Vielseitigkeit als bisher möglich. Darüber hinaus verbessert die Prozessrückmeldung die Leistungsfähigkeit einer Maschine weiter, indem Werkzeuge im kompletten Leistungsbereich genutzt werden können, mit der Sicherheit dass eine automatische Überwachung einen Unterbrechung des Zyklus zu gewährleistet, bevor etwas Katastrophales eintritt.
Die nahtlose Integration verschiedener Technologien und Bearbeitungen in einer einzigen Maschine kann vorteilhaft sein. Parametrische 3D-Programmierung, ausgefeilte Nachbearbeitung, Werkzeugverwaltung und Überprüfung auf der Maschine sind in immer mehr Betrieben üblich, da die Technologie erschwinglicher wird. Leistungsfähige Maschinen wurden entwickelt, um diese Technologie zu optimieren, was den Fertigungsprozess für wettbewerbsfähige Formenhersteller drastisch verbessert.
Die UNISIG USC-M50 ist ein leistungsfähiges, unverwüstliches Bearbeitungszentrum das hochpräzises Tiefbohren mit Bearbeitungsfunktionen kombiniert. So können Formenbauer viele notwendige Bearbeitungsprozesse in einer Aufspannung mit der im Formenbau erforderlichen Genauigkeit ausführen.
Die USC-M50 führt im Concourse Mould Werk in Ontario, CA Hochgeschwindigkeits-Planfräsen auf einer großen Form durch.