Feb
Nov
Hybrid Milling/Drilling Machine Reduces Total Mold Machining Time
- 2022
- Ampersand Milwaukee
As appeared in MoldMakingTechnology.com
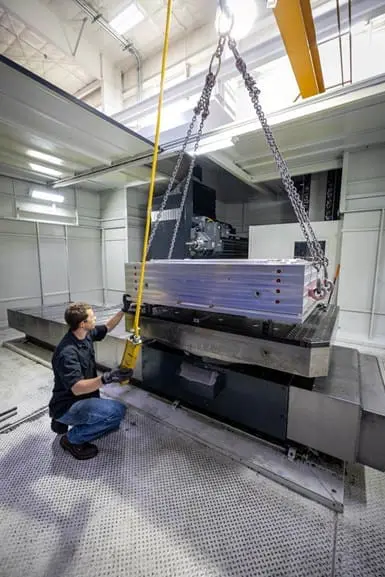
MSI Mold Builders (MSI) of Cedar Rapids, Iowa, and Greenville, South Carolina, specializes in designing and building large-tonnage prototype and production molds for use in the medical, packaging, agricultural, truck, appliance, power sports, heavy equipment, aviation and materials handling segments. For over 20 years, MSI has been firmly committed to lean manufacturing, applying Six Sigma and 5S principles to identify choke points, reduce waste, improve safety and quality, and increase productivity and customer satisfaction. A few years ago, the Cedar Rapids team identified the first step in their mold building process as a bottleneck, preventing the company from reducing lead times and increasing capacity.
MSI Mold Builders
Problem: Eliminate bottleneck at the front of mold building process where large blocks are squared, eye bolts are installed, and waterline and various holes are drilled.
Solution: Purchase of a five-axis Unisig USC-3M combination milling and drilling machine.
Results: Diverted 50% of traffic from an old gundrill, reduced total machining time per tool by 10-15% and increased mold output by 5%.
Reduce Setup, Boost Productivity
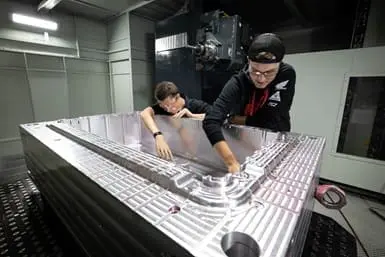
“The core and cavity sides of our molds tend to be very large blocks that average 8,000 pounds [3,629 kilograms],” explains Chris Waterbury, MSI Cedar Rapids production manager. “Given their size and weight, these blocks are difficult to handle, so our first step is to square the blocks and then install eye bolts, which allows us to move blocks through our manufacturing process quickly and safely.” Historically, blocks would first go into a horizontal boring mill to be squared on all four sides; then, they’d be moved to the gundrill to have the eye-bolt holes drilled. This process typically required six setups between the two machines, and each setup typically took 30-60 minutes. “What we wanted was to find a single machine where we could both square our blocks and drill and tap for eye bolts — ideally using fewer setups,” he says.
“Roger Klouda, our president, is always looking for new and innovative ways to improve our operations,” adds Steve Hoeger, MSI COO. “As MSI continues to grow, we need to keep improving our operating efficiencies. So, as luck would have it, at a show, Roger saw a new Unisig product that he thought would help us shorten lead times, increase capacity, and improve safety and quality — an all-in-one machine that was specifically designed for moldmaking and unique in the size blocks it could handle.”
The machine in question was part of the USC-M series, a group of machining centers from Unisig that had indeed been designed to meet the needs of the moldmaking industry and were able to both mill and deep-hole drill. Two of the six machines in this family have a universal spindle that both mills and gundrills, while the other four have two spindles — one that mills and the other that gundrills and produces deep holes using the BTA process, which is even faster than gundrilling.
The model that interested the MSI team was the USC-3M, a 3+2 axis machine that can rough mill but also gundrill to a depth of 71 inches/180 centimeters on each side, as well as drill angled holes at +30° and -15°, which provides more flexibility where waterlines are placed, helping moldmakers improve cooling and reduce cycle times for their molder customers. Additionally, the machine has a rotating table that is 63 × 78 inches/160 × 198 centimeters and can hold a block of up to 66,150 pounds/30,005 kilograms while providing travel of 122 inches/310 centimeters in the X-axis, 69 inches/175 centimeters in the Y-axis and 51 inches/130 centimeters in the Z-axis.
“We were excited about this machine because it looked like it would do exactly what we needed at the front-end of our process and greatly improve lead times,” says Waterbury. The team visited Unisig headquarters outside Milwaukee to learn more.
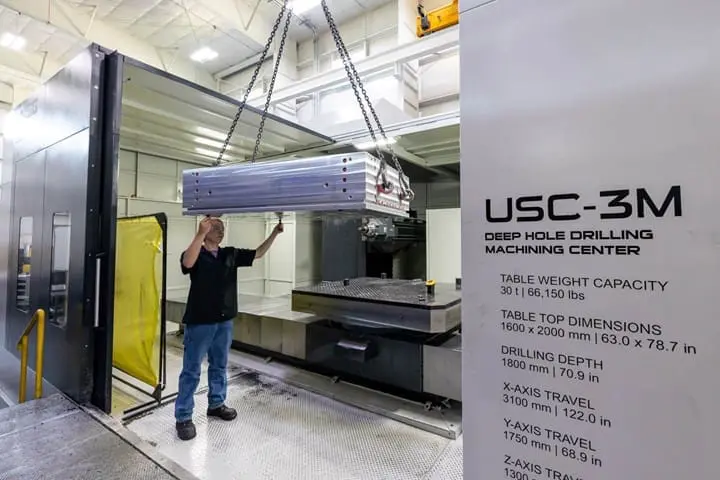
Experts in Deep-Hole Drilling
Unisig was founded in Elgin, Illinois, in 1981 and relocated to Menomonee Falls under its current ownership in 1995. In 2011, Unisig set up Unisig GmbH in Germany to better serve European customers. The company offers complete deep-hole drilling systems, including machines, tools and automation — all designed and built in the U.S. and serviced by a global sales and service organization. Throughout its history, Unisig has built expertise in deep-hole drilling, which is illustrated by the breadth of equipment it produces — from machines that can drill delicate 1-millimeter/0.040-inch-diameter holes in titanium medical components, to machines that can drill 500-millimeter/20-inch-diameter holes over 10 meters/30 feet deep in massive, high-strength steel forgings for the power industry.
“Our purpose is to be the answer to any deep-hole drilling problem in any industry anywhere in the world,” explains Anthony Fettig, Unisig CEO, who started as an engineer at the company in 1994. “To accomplish that, we listen carefully to our customers to understand what they need, then we build a product in line with their vision. Plus, we invest in ourselves to keep expanding and growing this market organically.”
For example, he recalls that no one had ever heard of the company when Unisig first considered getting into the moldmaking industry. However, after speaking with mold builders for several years, Unisig recognized that there was pent-up demand for a machine that could mill and drill well. “What struck us was that existing options were underpowered and couldn’t offer aggressive CNC machining,” continues Fettig. “We knew our priority was to engineer a machine that could mill aggressively and still had enough power and sophistication to drill fast, yet also had the accuracy that would enable you to trust the machine. In addition, our goal was to help mold builders get more work done with less setup so they could cut calendar days off their production schedule. That, in turn, would enable them to be more flexible on engineering changes by not having to reprocess molds multiple times as they moved through production.”
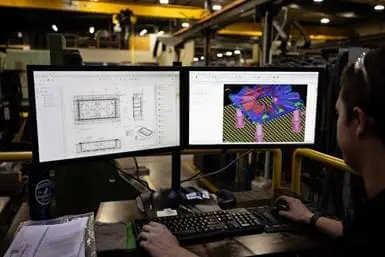
Unisig introduced its first USC-M series machines in 2006 — the M is for mold building — and introduced its first models (the -3M and smaller -2M) with universal spindles that could mill and drill in 2018 when indexable gundrills became viable. “We have a bias toward clean, simple-to-use and very capable machines because if you get the foundational things right, then you have a competitive advantage,” adds Fettig. “There’s a reason our headstock weighs what it does and why we engineer powertrain dynamics and frame stiffness/rigidity the way we do, as these aspects are really important to get right for effective milling. Our USC-3M has a 30-ton table capacity. It’s a very big, strong machine whose weight capacity is much higher than a typical horizontal boring or milling machine. However, we felt it needed that, as well as very good reach and very high volumetric accuracy, to open up opportunities for our customers to process molds differently. Some people think we overbuild our machines, but we believe we’re taking our massive experience in deep-hole drilling and using it to futureproof our products against changes.”
Fettig recounts his deep respect for the mold building industry and how discussions with mold building customers helped Unisig improve its own manufacturing operations. “Moldmakers are very good at machining. Their influence while we developed the USC-M series inspired the adoption of technologies in our plant, such as modular fixturing, offline tool setup and full process simulation, which helped us be more productive. They totally changed the way we think about machining, and what we learned from them made us a better company.”
Reduced Setup Pays Off
MSI ordered its new USC-3M model with a standard 60-position toolchanger, Heidenhain controllers and glass scales standard; no additional customization was added. The machine has been operating since February 2021, and the MSI team has already seen marked improvements in productivity.
For starters, every new mold that passed through the Cedar Rapids facility previously spent time on the company’s single gundrill. Now, 50% of that volume — all the biggest mold blocks — has been diverted to the Unisig, where blocks are squared and eye-bolt holes are drilled and tapped. As a result, MSI estimates that all the setup time it previously expended to machine each side of the block and to move blocks back and forth from one machine to another at the start of its process has been reduced to a single setup on the Unisig, saving 10-15% of the total mold machining time, which has enabled MSI to increase its overall capacity by a minimum of 5% each year.
“We’ve absolutely seen an impact on our process,” says Waterbury. “Conservatively, that Unisig saves us six to 10 hours of setup time in the first step of our operation. That helps reduce errors and improve quality, plus it’s much safer not moving those big blocks around multiple times. The machine’s rotating table is a big benefit, and its ability to handle big blocks and drill to depths of 71 inches per side without changing setups is a real time saver. We also really like its large toolchanger. It all adds up to fewer setups, and its size and capabilities are really good fits with what we do here.”
“We hadn’t specifically been looking for a particular kind of machine,” adds Hoeger. “Rather, we just wanted to find ways to multitask to increase our business capacity and solve the problem of how to get our biggest blocks ready to go to the next step. This machine has done all that for us, and we’re very happy with its capabilities. It’s a multifaceted machine that solves our bottleneck and meets our needs. Plus, we really like that Unisig is close by in Milwaukee if we have a problem or need a part.”
Why should a moldmaker considering a hybrid milling/drilling machine purchase a Unisig? “We mill better, we drill faster, our volumetric accuracy will enable them to trust the machine, and we have the reach and travel to enable them to hit all four sides of the block if they want so they can work from the center of the table, not the corners,” says Fettig. “Also, because we listen to our customers and have vast experience in deep-hole drilling that no one else can touch.”
Landscape Photo Credit: MSI Mold Builders/Creative Technology Corp.
Oct
UNISIG Unveils Next Generation of UNE Gundrilling Machines
- 2019
- Anthony Fettig
Ideal for manufacturers focused on high-volume/low-mix or low-volume/high-mix production environments, UNISIG’s next generation of UNE Series gundrilling machines delivers operational flexibility, improved performance and effortless operation. Now available, the UNE Series is engineered and designed to simplify gundrilling for all those individuals involved in a facility’s manufacturing process. The UNE Series offers gundrilling solutions that are well-suited for various industries, including firearms, automotive, medical, energy, defense and aerospace.
With five models built from two frame sizes, the UNE Series can drill hole diameters from 1.4 mm to 40 mm and depths up to 3,000 mm. The compact frame construction saves valuable floor space as well. Each machine can fit in close proximity to a shop’s existing machining center, lathe or Swiss-style machine for efficient part-processing strategies. Built with quick and easy setup in mind, the machines are also small enough to be relocated when necessary. For added flexibility to grow with future production needs, all UNE models are robot-ready, allowing shops to add a robot whenever it fits into their budgets and production schedules.
“Our feature-rich UNE machines give customers a compact gundrilling solution equipped with the ability to grow alongside them,” said Anthony Fettig, CEO of UNISIG. “A lot of job shops and OEMs have the desire to automate but lack a timeline to do so. Our UNE Series gives them gundrilling benefits for today. It also provides them with security for tomorrow, knowing that they can further improve production by adding automation.”
Several innovative features contribute to the performance and productivity of the UNE Series. The single main spindle servo motor delivers the necessary horsepower for two-spindle machines. When power is applied in single-spindle mode, however, shops can produce holes with larger diameters, increasing their capabilities and adding the potential for new business without adding a new machine.
Unlike pressure-based coolant systems, the UNE Series features a programmable flow-based coolant delivery system designed to provide the right amount of coolant to the tool’s cutting edge. The end result for the operator means they can confidently predict tool breakage and spend less downtime recovering an interrupted process.
Powered by Siemens, UNE Series machines feature intuitive controls that give operators a full process picture at a glance on a rich color interface with touchscreen capabilities. The control’s heavy-duty buttons also function when operators are wearing gloves.
Ergonomically designed and engineered with the building owner and operator in mind, UNE machines offer an automated door option, which can benefit companies with or without automation. “Adding an automated door eliminates the repetitive task of opening and closing machine doors,” said Anthony. “Not only does this reduce fatigue, but it improves throughput and gives the operator an opportunity to focus on adding value in other areas.”
All UNE bases are FEA optimized and machined on five sides in single setup for the highest overall precision. This allows for simplified installation with no foundation work required, and 3-point leveling on machines rated up to 1,000 mm length.
UNE Series Overview:
- Three two-spindle models available with maximum hole diameters of 12 mm, 20 mm and 32 mm. Hole diameters even greater when used in single-spindle mode
- Two single-spindle models available with maximum hole diameters of 25 mm and 40 mm
- Five rated workpiece designation options between 750 mm and 3,000 mm
- Solid-carbide, brazed and indexable gundrill tools
- Automation ready
Jun
UNISIG Gundrill Grinder | Video
- 2021
- Philipp
End the guess work and sharpen drills in as little as 5 minutes with continuous high precision as the drill tip can be inspected on the big screen monitor while still clamped for grinding.
Continue reading ““UNISIG Gundrill Grinder | Video”“
Apr
Time to Rethink Resharpening Gundrills
- 2018
- Anthony Fettig
By Eric Krueger and Ryan Funk, Engineering Team, UNISIG
Originally posted in Manufacturing News
The modern gundrill is an engineering marvel, a well-designed piece of equipment that does one thing exceptionally well. A new gundrill will produce round, straight holes with enhanced cylindricity even at its deepest points. And it does all this while simultaneously providing a fine I.D. finish and excellent tool life.
Like all tools, gundrills wear out, typically after drilling around 1,000″. While a talented operator can still drill a hole with a worn gundrill, it will more often result in a loss of hole tolerance and finish at best. As gundrills wear, they require more thrust and torque while producing more run-out and experiencing greater drift. A dull cutting edge will produce irregular chips, which in turn cause spikes in coolant pressure – sure signs that failure is imminent.
Unlike some tools, gundrills are excellent candidates for resharpening. When performed correctly, the same gundrill can be resharpened to perform as well as a new drill as many as 8 to 10 times. The only significant difference between a resharpened gundrill and a freshly produced tool from the OEM is a slight back taper, an issue only for shops that require tolerances far beyond most manufacturers’ needs – all other shops can simply account for the ever-so-slightly reduced tool diameter. Otherwise, the only visible difference will be seen in the length of solid carbide on the gundrill’s tip.
Even coated drills can be sharpened. Naturally, this will reveal the raw carbide on the face, but this does not impact performance. The coating will remain on the wear pads and continue to improve the gundrill’s size control and ability to leave behind a finished surface. Tool life will be impacted, but the only other option is having it fully resharpened and re-coated by the OEM, which will likely be less cost effective.
Manufacturers have several options for resharpening their gundrills. For specialized gundrills, such as twin-flute tools and those intended for ultra-high-feed applications with chipbreakers below a coating, resharpening is something that only a gundrill’s OEM can do. A local sharpening service will likely have the proper equipment, but this requires having redundant tooling and factoring in lead time and transportation costs.
However, both of these methods result in a loss of process intelligence. The grinding process can offer valuable information manufacturers can use to optimize their gundrilling applications. As a result, more manufacturers that use gundrills are choosing to resharpen their tools in-house.
The main risk of performing resharpening operations in-house is poorly sharpened gundrills. Without the correct tip geometry, gundrills do everything worse: size control, roundness, cylindricity, finish, chip control, straightness and depth all negatively impact workpiece quality and result in significantly diminished tool life. This will cause operators to reduce feedrates or change out tools more frequently to achieve the necessary tolerances and out of fear of catastrophic tool failure.
Modern gundrill grinding systems make it easy to avoid these consequences. For the greatest advantage, one needs the full system. That means a grinder, the appropriate gundrill fixture and equipment for calibrating and inspecting the drill tip.
A basic, high-precision manual tool grinder is used as a platform for these systems, though the length of some gundrills necessitates a reinforced table for sufficient accuracy. Choosing a fixture can be more complicated, as gundrills can be ground in two different ways. Sweep grinding leaves behind a gradual transition between elements of the tip’s geometry, while facet grinding creates distinct geometry. UNISIG typically recommends facet grinding, because the slight increase in tip strength produced by a sweep grind is outweighed by the repeatability and greater ease of inspection offered by facet grinds.
The final piece of advanced gundrill grinding systems involves a digital inspection camera capable of viewing and storing magnified images. Ideally, this will allow the user to perform measurements and identify flaws without taking the tool out of the fixture. In addition to allowing for highly precise grinding, this inspection is vital for process optimization.
Process optimization capability is the real added value conferred by performing gundrill resharpening in-house. Frequent inspection allows for the maximization of tool life. Shops become familiar with the wear patterns created by a given application and may find they are replacing gundrills too often. If a gundrill tip has even wear across its entire cutting edge, it could easily have many hundreds of inches of life left, something that will only become apparent with repeated inspections.
In-house gundrill resharpening also ensures that shops can obtain the best tip geometry for their given applications. Whether it is uneven or unexpected wear, or the sudden appearance of chips in the cutting edge, once a shop identifies an irregularity, they can then adjust speeds and feeds to optimize the process. The inspection equipment even makes working with tooling OEMs easier, since shops can send them a measurement set and picture of a tool when asking for advice on how to improve the geometry.
With more experience, it becomes possible to tie a wear condition back to the process. For example, if there is a visible build-up along the cutting edge, it is often because the rotational speed is too slow. Conversely, if the edge is wearing faster than the tooling supplier’s data suggests, the tool is likely spinning too fast. Meanwhile, a chipped cutting edge suggests the feedrate was too high. With this know-how, shops can optimize the process and avoid future problems.
Fortunately, modern gundrill grinding systems make developing this know-how easy to achieve; in fact, the process usually takes longer to describe than it does to perform. After clamping in the gundrill, an operator can use geometry data from the tooling supplier to calibrate the camera. With the latest human-machine interface software, this can be as simple as drawing a line on the screen to establish the known gundrill diameter for repeatability purposes.
After calibration is complete, grinding can begin. The grinding wheel, turning in the direction toward the drill edge, makes contact with the drill tip after the operator confirms the correct rotational and X- and Z-axis orientations. A standard starting point grind will begin with the tip angled at +30° horizontally and +15° vertically with the rotation at +5°. The Y-axis is used to hold the tip to the grinder while feed is performed along the Z-axis at a rate of about 0.002″ per pass.
Some gundrills include an outer secondary angle parallel to the front cutting edge where the primary and secondary angles meet. It is critical that this primary facet is relatively narrow, since too much width will increase heat production and, consequently, reduce tool life. The operator next moves to the inner relief facet by moving the grind fixture -20° vertically in the opposite direction from the primary angle. This movement results in the formation of a point position with a length that is exactly 1/4 of the drill’s diameter, or the “D/4″ position, but other lengths may be necessary depending on the material.
Next, the operator moves to the front clearance, a facet with a point close to – but not touching – the front cutting edge. With standard gundrill tip geometry, a 0° horizontal angle and rotation as well as a +26° vertical angle will provide the correct position. While cutting performance improves the closer this point gets to the cutting edge, optimal edge strength requires placing the point slightly behind the edge. If a tip’s geometry requires an outer secondary angle, the front clearance facet’s point should meet it. Otherwise, the point of the facet is placed between 0.02″ and 0.03” behind the front cutting edge.
The final step on the grinder provides the oil dub-off, a facet with an edge tangential to the flute of the gun drill. Operators position the grind fixture at -30° horizontally, +25° vertically and +65° rotationally. The gundrill tip then feeds into the grinder at a rate that prevents cutting into the front cutting edge. The optimal angle meets the inner relief angle at the corner opposite the gundrill’s outside diameter.
After grinding is complete, the operator can use a hand chamfer to create additional clearance for optimal performance. The finished gundrill is now resharpened and ready for use – a process that takes fewer than 10 minutes. Given the ease of use and the significant process optimization opportunities, it is time to re-think gundrill resharpening.
Reposted with permission.