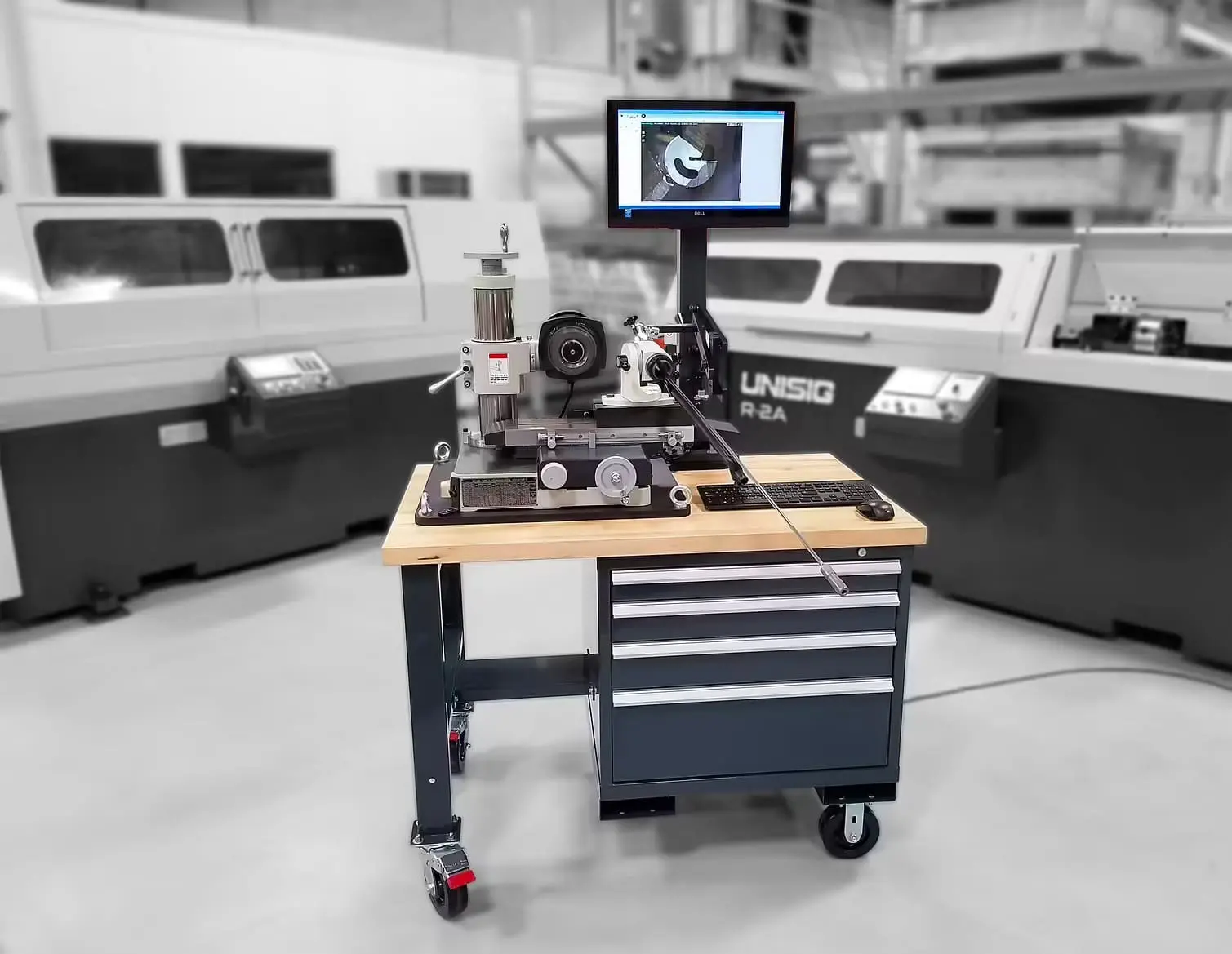
Increase Productivity and Profit with Gundrill Resharpening
- Posted on
- Ampersand Milwaukee
Gundrilling tools properly applied create impressive holes with very close diameter tolerances and roundness, good surface finishes and — of course – holes much straighter and deeper than those accomplished with a twist drill.
However, when the drill is used long enough to become dull, chip formation will change, hole quality will deteriorate, and eventually the gundrill will fail. It’s important to stop drilling before failure to avoid the risk of scrapping the part or trying to retrieve a piece of broken carbide out of a deep hole. Gundrill failure also eliminates any chance to resharpen the tool.
Gundrills typically have a slight back taper along the head, so after each sharpening there is a minor change in drilling diameter. When the drill has been sharpened too many times, the head length and wear pads are too short to guide the tool, and it needs to be replaced.
Most types of gundrills are excellent candidates for resharpening, which can be done approximately eight to ten times. In most cases resharpened gundrill performance will be similar to that of a new tool. Even coated gundrills can be resharpened, since the coating on the wear pads that burnish the holes while drilling remains, which is often the primary value of the coating. Twin-flute tools and those intended for ultra-high-feed applications with chip breakers below a coating usually require OEM resharpening.
In a majority of cases, however, a dedicated gundrill grinding system enables shops to accurately resharpen gundrills in-house to save on labor, transportation and tool availability costs. Additionally, the understanding of the gundrilling gained by sharpening drills will encourage improvements in how the tools are applied.
Sharpening a gundrill will take less than 15 minutes with a good grinding system that includes step-by-step instructions and is often performed by a gundrilling cell operator while the machine is drilling with other tools. The best grinding systems also provide information about tool performance before sharpening. Familiarity with normal wear patterns will enable a shop to adjust drilling parameters, extend time between resharpening operations and increase productivity and profits with higher feed rates, improved quality, better machine utilization and fewer unexpected failures that disrupt production.
A dedicated gundrill resharpening system includes a manual tool grinder, a fixture designed to hold the drill for grinding and a digital inspection camera to view and store magnified images of the drill tip. The images enable users to perform measurements and identify problems without taking the tool out of the fixture. Users can then learn to identify the causes of extreme, uneven or unexpected wear or chipping and adjust speeds and feeds to optimize their cutting processes. A shop also can use saved drill images to communicate wear modes to the drill manufacturer, who can provide advice on ways to limit wear and extend tool life.
Given the ease of use and the significant process optimization opportunities the process provides, many shops should consider adding in-house gundrill resharpening capability to save time and maximize their tooling investment.