Jul
BTA Drilling: Brazed Versus Indexable Tooling
- 2023
- Ampersand Milwaukee
Deep hole drilling applications can be approached in several ways, but one of the most effective methods is often BTA drilling. BTA stands for Boring and Trepanning Association, although it is sometimes referred to as STS or Single Tube System drilling. Unlike gun drills or twist drills a BTA drill features internal chip removal, which has advantages in both productivity and hole quality.
The BTA drill head has multiple carbide cutting edges and guide pads mounted to it. Open spaces are designed into the head for chip removal, and chips are evacuated through the drill tube the head is threaded onto. Pressurized coolant surrounds the drill head in operation, and is key to forcing chips through the head and out the drill tube. This method of chip evacuation allows for a very clean and reliable process with excellent surface finish and high drill feed rates – typically 5-7 times faster than gundrilling at the same diameter. No peck cycles or feed interruptions are needed, resulting in reduced machine time while drilling extended depth-to-diameter ratios even greater than 40:1.
BTA drills are generally available in two forms: brazed or indexable; and tool selection is dependent upon several factors. As the name implies, brazed tools involve brazing a carbide insert and guide pads onto a steel body, while indexable BTA drilling tools have carbide inserts either directly mounted to the head with a retention screw or seated in a cartridge that is mounted to the tool.
Hole diameter is the initial consideration when determining whether to use brazed or indexable BTA drills. For small hole diameters – generally 12 to 20 mm in diameter – brazed tools are often the first choice as it’s difficult to make small inserts and screws strong enough to withstand the torque and forces of BTA drilling. (Manufacturers of BTA drilling tools continue to make improvements in indexable BTA heads as small as 8 mm in diameter, however).
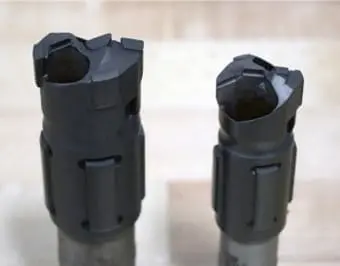
Brazed tools offer extremely close tolerances and excellent surface finish as the insert and guide pads are mounted and then ground to the specified diameter, providing almost perfect concentricity and cylindricity. Ease of use is also a benefit – simply attach the head to the drill tube and discard it when it has dulled or failed. If you experience a tool failure, the investment in drill head isn’t as costly as repairing or replacing an indexable drill head. Finally, an indexable BTA head can only be as accurate as the tolerance of the inserts themselves; but a brazed head has been ground to a very precise tolerance from the manufacturer.
By contrast, hole diameters starting at approximately 20 mm favor indexable tools, primarily for economic reasons. Replacing larger diameter brazed tools is expensive, whereas indexing an insert and guide pads gives an easy extension on the tool’s life. Indexable insert manufacturers also offer an exhaustive range of carbide grades, coatings and chip breakers for application-specific advantages.
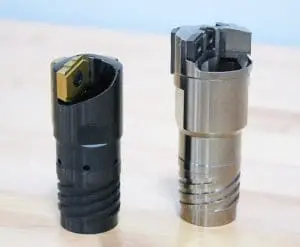
The placement of the indexable inserts on BTA drill head varies by diameter and by manufacturer, and can include one or multiple inserts mounted directly to the head or set in a heat-treated cartridge which is then mounted to the head. Guide pads are typically mounted the head to counter the drilling forces and burnish the hole during drilling. Indexing, or rotating, a direct-mounted insert is as simple as loosening the retaining screw and turning the insert to expose a fresh cutting edge. If the insert and pocket were made with tight tolerances, your cutting diameter should remain reasonably consistent.
Cartridge-mounted inserts, however, typically incorporate a shim or other adjustment system to allow for a much more precise diameter setting after indexing inserts and guide pads. This process does require additional equipment, however, such as a micrometer and stand or tool presetter – as well as the skills needed to accurately make the necessary adjustments.
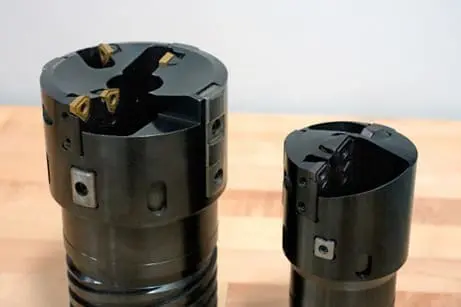
Whether you select brazed or indexable BTA drills for your deep hole drilling application, you will be rewarded with high feed rates and process reliability, along with minimal centerline deviation and excellent hole quality.
To learn more, contact UNISIG about its complete portfolio of BTA drilling machines, drill tubes, tools and BTA durable tooling.