When the manufacturing engineering team at medical device manufacturer ConMed, needed to find a way to pull significant costs out of production, he saw an opportunity to bring bone drill holemaking in house
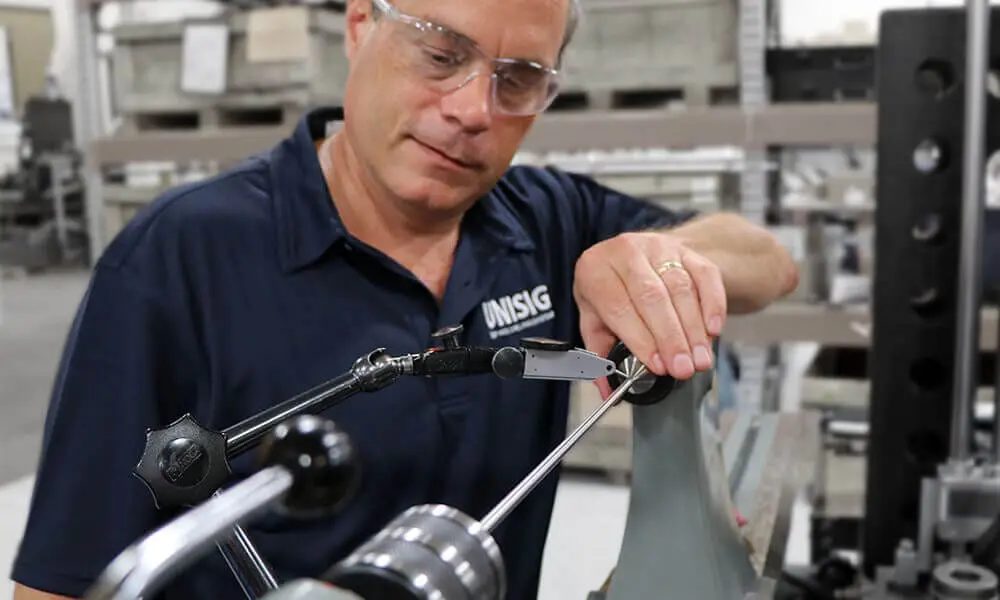
Drilling Down to the Smallest Diameters | Case Study
- Posted on
- Anthony Fettig
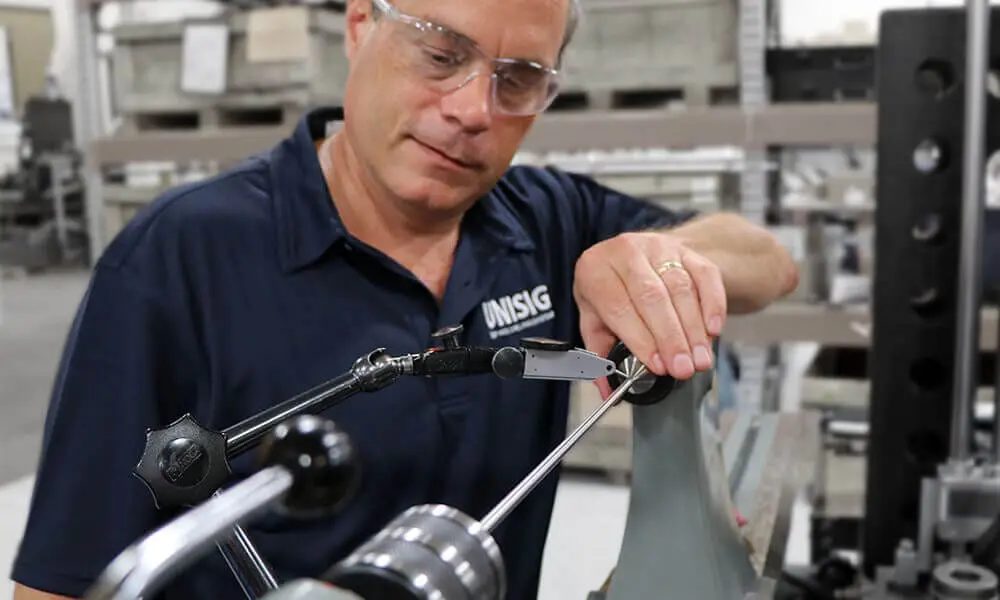
When the manufacturing engineering team at an international surgical equipment manufacturer needed to find a way to pull significant costs out of production, they saw an opportunity to bring bone drill holemaking in house. The parts, however, presented a significant challenge, with small diameters, thin part walls, and approaching depth-to-diameter hole ratios of 100:1. The department manager and his team weren’t sure that gundrilling could hold their required tolerances and give them the control of accuracy that they needed.
Medical tooling components, and similar applications with extremely small diameters, are on the edge of what is possible with small diameter deep hole drilling. These diameters are produced with gundrilling, a process which uses a single effective cutting edge to produce deep holes with high pressure coolant and effective chip removal, reaching depth-to-diameters that other processes cannot handle. Typically, counter-rotation of the tool and workpiece is used for maximum concentricity of the finished hole, performed on a dedicated gundrilling machine equipped with smart controls to take any guesswork out of the process.
Holes in the extremely small range present additional challenges compared to more common depths and diameters. Often, workpiece dimensions and shapes result in thin walls and non-uniform sections, with extreme precision requirements, and demanding a consistent, reliable process in order to produce successful parts. Gundrills in this range of diameters require additional support to sustain rigidity, and process development is essential for developing ideal drilling speeds and feeds. Control and feedback of the operation is critical.
The manufacturing engineering team considered different solutions for their in-house production. When they began their search, they had no experience with gundrilling, and were looking to confirm that the process could hold their tight tolerances, while ultimately finding a solution that wouldn’t upset their production.
“The process collaboration with UNISIG gave us confidence that we could produce this part and hold the runout. The team at UNISIG said ‘There shouldn’t be any reason we can’t do it the way you want’ after evaluating our process and demands. And they made it happen.”
The surgical equipment manufacturer ultimately decided on the UNE6 gundrilling machine, designed specifically for the extremely small hole diameters that his parts required.
They worked with UNISIG’s engineering and technical teams to develop a solution that fit their demands without compromise through detailed process collaboration. The result was a standard UNE6 machine, with additional tooling and accessories to ensure the accuracy of the process, and in-depth training with the manufacturer’s operators and engineers, enabling them to confidently begin production immediately following installation.
UNE6 gundrilling machines are compact, accurate, and have intuitive operation, for parts requiring holes up to 0.25 in [6 mm] in diameter, using the counter-rotating gundrilling process. To maintain the optimal drill speeds and feeds for the operation, the machine uses a high speed, integral motor spindle, reaching 20,000 rpm, to provide ample power while also reducing vibrations at sustained high speeds. A high-pressure coolant system is required to manage the required 3,000 psi of coolant needed to flow through the extremely small tool. Additionally, application specific support and fixtures were developed to support short drills, and clamp on the outside diameter of the part, for very high repeatability.
Capable gundrilling for extremely small diameters has opened up a whole new realm of possibility for medical and surgical equipment manufacturers, who face similar challenges in both accuracy and production. Using a proven gundrill process after turning enables a profitable, reliable solution in the challenging small diameters of medical tooling and components.
The manufacturing engineering team uses process monitoring on the machine’s interface to keep an eye on the drilling process, ensuring their accuracy is upheld, while keeping up demanding production. The machine handles 2 families of products with over 30 individual part numbers, and enables them to keep up with demand, while producing competitive parts for the medical industry. They currently run 2 shifts, alongside a screw machine, to keep up with demand while maintaining confidence in their parts. The department manager explains that their cycle time has been cut in half, saving them significant costs, and providing a controlled solution. “It’s so easy for our operators to use”, he states, “the machine basically runs itself.”